Simons + Valiani
I'd rather show off what the machine can do rather than the machine - let the customer think it's all done by candle light with a sharpened bit of flint if they like.
How do you work out 'higher quality mounts at lower cost'? How long will it take to recoup your outlay - inc interest. What about the new/increased running costs?
I'd be putting my prices up, not down and all mounts cut with the machine would be priced as if I'd done them by hand.
How do you work out 'higher quality mounts at lower cost'? How long will it take to recoup your outlay - inc interest. What about the new/increased running costs?
I'd be putting my prices up, not down and all mounts cut with the machine would be priced as if I'd done them by hand.
-
- Posts: 11003
- Joined: Sat 25 Mar, 2006 8:40 pm
- Location: Devon, U.K.
- Organisation: The Dartmoor Gallery
- Interests: Lost causes, saving and restoring old things, learning something every day
- Location: Glorious Devon
-
- Posts: 11003
- Joined: Sat 25 Mar, 2006 8:40 pm
- Location: Devon, U.K.
- Organisation: The Dartmoor Gallery
- Interests: Lost causes, saving and restoring old things, learning something every day
- Location: Glorious Devon
Hi John,Roboframer wrote:I'd be putting my prices up, not down and all mounts cut with the machine would be priced as if I'd done them by hand.
Exactly my thoughts too! I'd do a price list with charges per cut-out and for "special" graphics, etc. If ever there was a machine to make money, this has got to be it!
Mark
will be right by a window to start off with, then possibly if Daler get the heave-ho it'll be going where our 3m art supplies unit is near the workshop at the back of the premises.Not your average framer wrote:Hi Grahame,
I take your point, but you might need a barrier around it to stop meddling fingers, etc.
It's very visual when it's working and should be a a real crowd puller, if visible near a window.
going to discuss a rope barrier with the relevant parties.
Hooked cuts arent a problem. blunt blades generally cause a very ragged cut - hooking is a calibration problem and you should have embarrassed them by pointing it out.. In real world production as with all machines you calibrate - then fine calibrate over time to get as near perfection. Calibration is very straight forward and once you get to the sweet spot tends to stay there.Not your average framer wrote:I too have decided I want a Valliani. I asked a lot of questions and got a demo of the machine but I have a question which perhaps existing Valliani users can answer.
The demo mount had hooked cuts, which were easy to see on a very thin decorative cut-out strip, with so many people there I did not ask about this.
Can someone tell me if this is due to the blade needing changing or if this is something you have to live with?
Mark
As for the high tech aspect of a craft skill - I think my customer appreciate that I invest in the best equipment to give them a first class job.
any comments on my revamped wording?
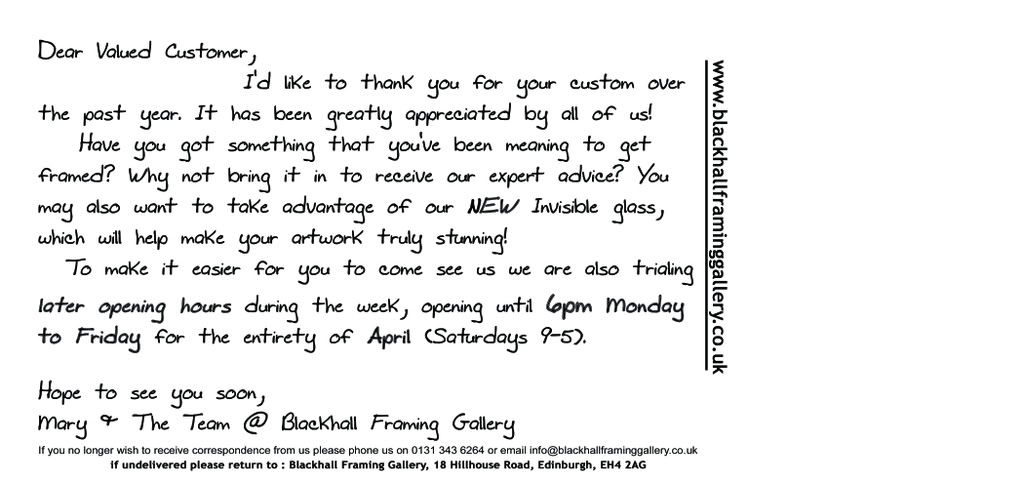
i really appreciate having somewhere like the forum that i can come crawling to, it stops us getting too polarised in our views on advertising and stuff!
NYAF, i remember you once posted a "health and safety" sign, i think i may adapt something similar,
but we've already got plans for the computer etc to be locked with a password so it can't be touched.
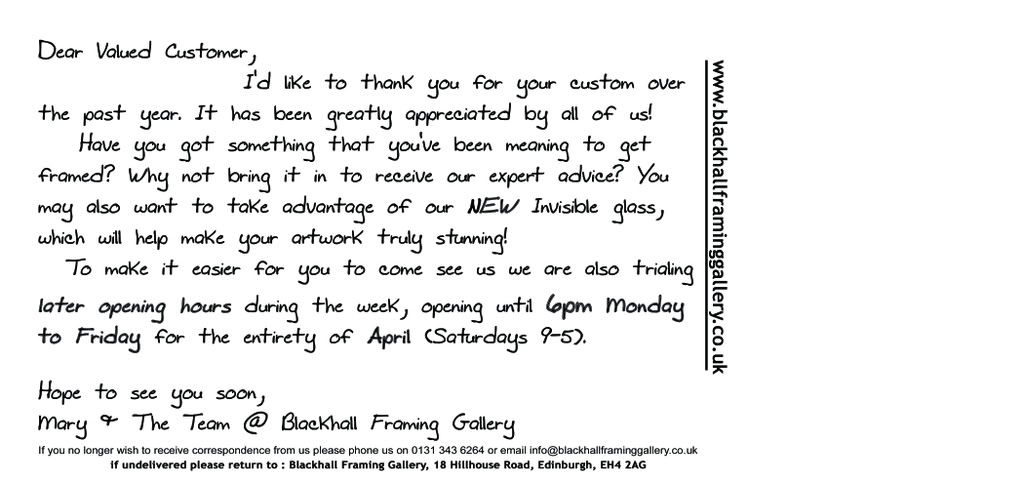
i really appreciate having somewhere like the forum that i can come crawling to, it stops us getting too polarised in our views on advertising and stuff!
NYAF, i remember you once posted a "health and safety" sign, i think i may adapt something similar,
but we've already got plans for the computer etc to be locked with a password so it can't be touched.
Grahame,
You are doing the right thing in promoting your new CMC to your customers. I have a couple of observations I would like to share with you from my experience.
1. Your customers generally will not be as excited as you are about your new CMC. Customers are concerned with themselves and are interested in how it will benefit them.
2. I would not put the machine in a place where customers can get near it. Mine is inside the workshop and occasionally I have invited certain people to watch it work. Some framers have theirs behind a glass window so customers can see it work.
3. Add at least 1 or 2 quid to your current price on every mat opening to help pay for the machine.
4. I would offer free designer corners on their purchase instead of a discount on the whole job. That will cost you nothing!
If you are hell bent on giving a discount, try giving a few quid off the job. I have discovered that I get a dramatically bigger response when I offer $20 off than 20% off. Many people actually thank me for sending them $20. You could scan a 10 or 20 pond note and print one side of it on a piece of paper and include that with your newsletter. You could also photoshop it to include your business name on the note.
Good luck with your promotion!
You are doing the right thing in promoting your new CMC to your customers. I have a couple of observations I would like to share with you from my experience.
1. Your customers generally will not be as excited as you are about your new CMC. Customers are concerned with themselves and are interested in how it will benefit them.
2. I would not put the machine in a place where customers can get near it. Mine is inside the workshop and occasionally I have invited certain people to watch it work. Some framers have theirs behind a glass window so customers can see it work.
3. Add at least 1 or 2 quid to your current price on every mat opening to help pay for the machine.
4. I would offer free designer corners on their purchase instead of a discount on the whole job. That will cost you nothing!
If you are hell bent on giving a discount, try giving a few quid off the job. I have discovered that I get a dramatically bigger response when I offer $20 off than 20% off. Many people actually thank me for sending them $20. You could scan a 10 or 20 pond note and print one side of it on a piece of paper and include that with your newsletter. You could also photoshop it to include your business name on the note.
Good luck with your promotion!
Thanks for the advice Ormond. Grahame tends to get a bit carried away in his enthusiasm, which is no bad thing for someone of his age. I take on board all your observations, but unfortunately as regards siting of the machine, the shop is the only option. The workshop is too small to take it without having to throw out a member of staff. It's long but narrow. We should be able to keep an eye out for customers and make sure someone is in attendance at all times when it is working. Might rig up some sort of rope barrier.
-
- Posts: 3485
- Joined: Mon 25 Jun, 2007 5:43 pm
- Location: The Shire
- Organisation: An Urban Myth
- Interests: I'll let you know if I get my life back.
- Contact:
Major disappointment across Wizard, Valiani, and Gunnar CMC's - rough bevels. Seems to be generic to the technology. Also, cuts ending in fine points were definitely on the tufty side...Not your average framer wrote:The demo mount had hooked cuts, which were easy to see on a very thin decorative cut-out strip, with so many people there I did not ask about this.
That said, customers are probably more likely to be "galloping horses" than framers, and the wow factor of the mount designs possible can't be denied.
Couple of things gleaned from the show:-
- This may be down to lack of product knowledge on the part of the distributor, but it appears that there is no way to import outlines created in Corel to the Wizard control software, so it will be an absolute no-no if Corel is your drawing "weapon of choice."
- Need to research it more, but the Gunnar "blade cartridge" system appealed to me far more than the Valiani "head swap" method, in terms of ease of use (comparable to the reasons why the Excalibur 5000 rotating turret is appealing to custom, low volume framers).
........Áine JGF SGF FTB
.Briseann an dúchas trí shuiligh an chuit.

It was more the software that swung it for us. Having seen John's (Merlin) machine in action, I changed from wanting a Gunnar to a Valiani. I need software an eejit can understand, because I have a member of staff who does'nt know one end of a computer from the other. I went to the show looking for a double-headed machine, but was struck by the simplicity of changing heads on the new Valiani MatPro. On top of that it was cheaper, which always wins over a Scots lass 

-
- Posts: 1102
- Joined: Fri 17 Mar, 2006 8:54 pm
- Location: Glandwr
- Organisation: Framing Mad
- Interests: Framing, watercolours & CCFC
- Location: Pembrokeshire
- Contact:
That's more or less what I do - mounts cost no less/no more than hand cut, but I don't charge extra for the standard designs in the gunnar, of which there are many dozens, and a free v-groove for a customer who spends over £50 (if they want one). Neither action costs me more than a minute of time over a standard rectangle or oval.osgood wrote:4. I would offer free designer corners on their purchase instead of a discount on the whole job. That will cost you nothing!
-
- Posts: 3485
- Joined: Mon 25 Jun, 2007 5:43 pm
- Location: The Shire
- Organisation: An Urban Myth
- Interests: I'll let you know if I get my life back.
- Contact:
Great tip from Gunnar: assuming that you are cutting a mount face-up, use the regular blade for the bevelled aperture in a "reverse bevel" action for the outside cut, if you get my drift. Assuming that this method is also possible for the Valiani, it should eliminate the need to purchase a 90-degree head. Realistically, for a small volume, bespoke operation, I don't see a real need for a 90 degree head other than the times when one is cutting multiple identical mounts from a single sheet. For one-off jobs, in practice it would be easier to cut the board(s) to size on one's sheet cutter first.Mary Case GCF wrote:I went to the show looking for a double-headed machine, but was struck by the simplicity of changing heads on the new Valiani MatPro.
'nuvver tip: for Valiani, better aperture cutting results on 8-ply board when the aperture is cut face-down.
........Áine JGF SGF FTB
.Briseann an dúchas trí shuiligh an chuit.

Now she tells me ! I only went and ordered the 90 degree head as an add-on. Could have saved myself some money there.Great tip from Gunnar: assuming that you are cutting a mount face-up, use the regular blade for the bevelled aperture in a "reverse bevel" action for the outside cut, if you get my drift. Assuming that this method is also possible for the Valiani, it should eliminate the need to purchase a 90-degree head.