Tapestry lacing
-
- Posts: 367
- Joined: Wed 03 Oct, 2007 1:37 pm
- Location: Shrewsbury
- Organisation: Sutherland Arts & Crafts
- Interests: Photography
- Location: Shrewsbury
- Contact:
Tapestry lacing
I have been asked to frame a tapestry using a shallow rebate ash moulding. The customer does not want any great protrusion at the back of the frame so I can only do this by folding the tapestry over a backing board and lacing it up.
I do not think that Art-bak will be rigid enough so is it acceptable to use mdf and a barrier layer card ?.
Also I do not have any suitable cord (?) or needles so can anyone recommend the right gear and a supplier. I presume the technique is similar to using a stretching frame and staples ie lace the two middles and then work outwards.
I do not think that Art-bak will be rigid enough so is it acceptable to use mdf and a barrier layer card ?.
Also I do not have any suitable cord (?) or needles so can anyone recommend the right gear and a supplier. I presume the technique is similar to using a stretching frame and staples ie lace the two middles and then work outwards.
Pat
-
- Posts: 1102
- Joined: Fri 17 Mar, 2006 8:54 pm
- Location: Glandwr
- Organisation: Framing Mad
- Interests: Framing, watercolours & CCFC
- Location: Pembrokeshire
- Contact:
Re: Tapestry lacing
Only if you want it to risk it going mouldy! Use acid free mountboard.The Crofter wrote:so is it acceptable to use mdf and a barrier layer card ?.
How deep is this moulding anyway? Personally I would have told the customer that the minimum rebate you could do that job with would be about 12-14mm - you can't squeeze a quart into a pint pot.
When you say 'tapestry', do you mean the woolly kind that are done on a sort of open weave fabric? For lacing these I use #0 nylon cord. For more delicate stuff, samplers, etc, linen thread is better.
As for not sticking out the back of the frame - what Spit said.
A lot of these things are framed touching the glass. Bad idea.
Nice method is to use a narrow beveled linen liner under the glass. gives a good 6mm spacing.
As for not sticking out the back of the frame - what Spit said.

A lot of these things are framed touching the glass. Bad idea.

Nice method is to use a narrow beveled linen liner under the glass. gives a good 6mm spacing.
Re: Tapestry lacing
That is the best way to mount needlework!The Crofter wrote: I can only do this by folding the tapestry over a backing board and lacing it up.
MDF is not suitable for this or anything else! Didn't you recently say that you are not using MDF any more?The Crofter wrote:I do not think that Art-bak will be rigid enough so is it acceptable to use mdf and a barrier layer card ?.
No, do not work from the middle outwards. Work from one side to the other, then when you are satisfied that you have all the lines in the needlework straight, fold the other two sides over the back and lace them together, beginning at one side and finishing at the other. use one length of thread. Thread need to be non-stretch and lighter in strength than the base fabric of the needlework!The Crofter wrote:Also I do not have any suitable cord (?) or needles so can anyone recommend the right gear and a supplier. I presume the technique is similar to using a stretching frame and staples ie lace the two middles and then work outwards.
Send me a PM with your email address and I will send you some comprehensive instructions!
-
- Posts: 367
- Joined: Wed 03 Oct, 2007 1:37 pm
- Location: Shrewsbury
- Organisation: Sutherland Arts & Crafts
- Interests: Photography
- Location: Shrewsbury
- Contact:
The customer specified that she wanted the tapestry framed without glass and in 38mm plain ash moulding.
I completed the job this morning using very thin plastic coated hanging wire as the lacing material. The wire was terminated & tensioned using crimps.
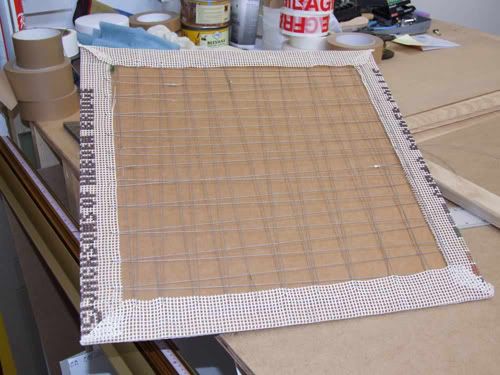
The tapestry is supported by Art-bak conservation. Unfortunately I forgot to take a picture of the original before framing but the stitching finished after the second row of the border. Lacing and manouvering the tapestry so that the frame rebate exactly matched the border was a bugger but I think it turned out ok.
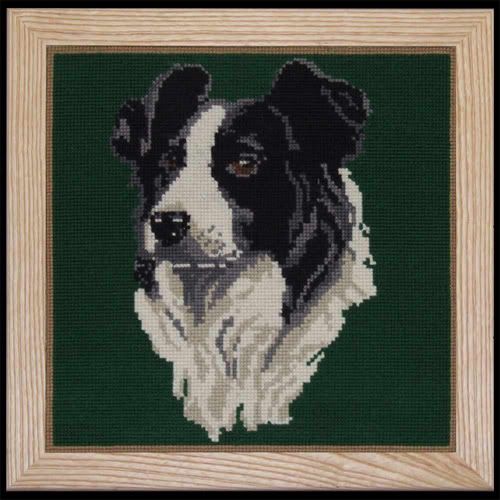
The Art-bak did bow quite a bit but I sealed the back with another piece that bowed inwards so hopefully the the package will reamin fat.
Anyway the customer was delighted with the result and the £23.80 bill....
I completed the job this morning using very thin plastic coated hanging wire as the lacing material. The wire was terminated & tensioned using crimps.
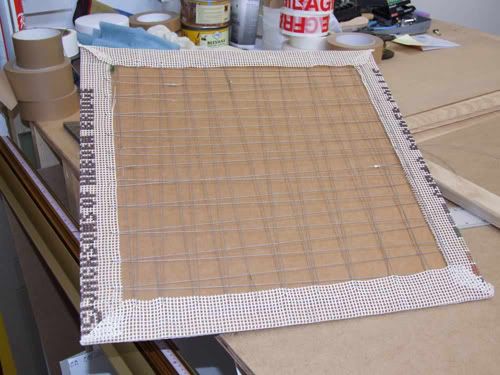
The tapestry is supported by Art-bak conservation. Unfortunately I forgot to take a picture of the original before framing but the stitching finished after the second row of the border. Lacing and manouvering the tapestry so that the frame rebate exactly matched the border was a bugger but I think it turned out ok.
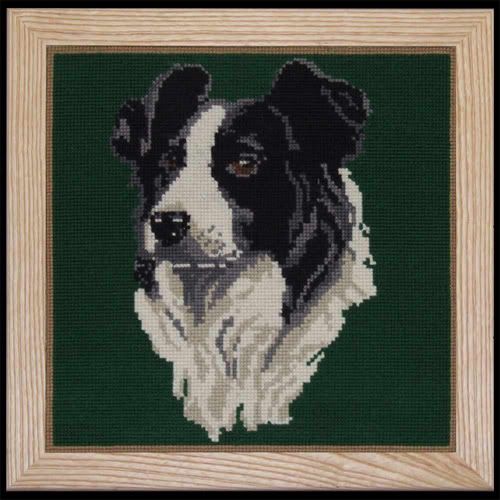
The Art-bak did bow quite a bit but I sealed the back with another piece that bowed inwards so hopefully the the package will reamin fat.
Anyway the customer was delighted with the result and the £23.80 bill....
Pat
-
- Posts: 367
- Joined: Wed 03 Oct, 2007 1:37 pm
- Location: Shrewsbury
- Organisation: Sutherland Arts & Crafts
- Interests: Photography
- Location: Shrewsbury
- Contact:
Just put the figures into my database at home so slight difference.
Final tapestry size approx 420mm square
Moulding £2.30/m
Total material cost £4.09
Profit £19.39
This includes moulding markup of x2 and backboard markup x3
The job took an hour which I charged at my normal rate of £15/hr.
I realise the price is way below what most of you would consider realistic but things are a bit different for me up here. I have set my prices at a level that I know will bring in local business. If I go too high then the few customers I have will contemplate going to Inverness. This has nothing to do with the value of the work but a perception that I am "expensive". Not logical but I have seen other people suffer from this problem.
My overheads are pretty low, just £90 per month for my contribution to the rates and we split the bills 50/50. I do pay a lot for delivery and my glass price is 3x the norm. However I have adjusted my markups to compensate for delivery and keeping stock that may never sell.
Keeping my prices at a "competative" level ensures that I do get customers through the door which helps spread the word. Up here word of mouth is the best advertising you can get.
My own circumstance are probably very different. The gallery work supplements my pension and I do not rely on the extra work to survive.
As time progresses I hope that selling my own work will be a better earner, certainly the profit will be greater as I can add the value of my art to the framing costs.
Final tapestry size approx 420mm square
Moulding £2.30/m
Total material cost £4.09
Profit £19.39
This includes moulding markup of x2 and backboard markup x3
The job took an hour which I charged at my normal rate of £15/hr.
I realise the price is way below what most of you would consider realistic but things are a bit different for me up here. I have set my prices at a level that I know will bring in local business. If I go too high then the few customers I have will contemplate going to Inverness. This has nothing to do with the value of the work but a perception that I am "expensive". Not logical but I have seen other people suffer from this problem.
My overheads are pretty low, just £90 per month for my contribution to the rates and we split the bills 50/50. I do pay a lot for delivery and my glass price is 3x the norm. However I have adjusted my markups to compensate for delivery and keeping stock that may never sell.
Keeping my prices at a "competative" level ensures that I do get customers through the door which helps spread the word. Up here word of mouth is the best advertising you can get.
My own circumstance are probably very different. The gallery work supplements my pension and I do not rely on the extra work to survive.
As time progresses I hope that selling my own work will be a better earner, certainly the profit will be greater as I can add the value of my art to the framing costs.
Pat
aha, that would explain it. i realise it is often grim up north for the Picture Framer. you've alot fewer overheads than us to say the least... we have staff, exorbitant rates, electricity, water, gas, and mortgage, oh and a CMC to pay off.
i'm pleased to see you are making a profit though, it just didn't seem to look like it from our point of view
i'm pleased to see you are making a profit though, it just didn't seem to look like it from our point of view
Pat,
When lacing any type of needlework the lacing thread need to to be weaker in strength than the threads that make up the ground of the needlework. Wire would not be weaker and is not a good choice for this. Something like crochet cotton would have been much more suitable.
Your pricing system has stunned me! I would have charged around five times as much. I have heard the story about how tough things are in an area many times in the past and that may be so, but my advice is to try to charge a price that is more in keeping with what other framers charge.
I think your material cost including wastage would be much higher than you have calculated!
When lacing any type of needlework the lacing thread need to to be weaker in strength than the threads that make up the ground of the needlework. Wire would not be weaker and is not a good choice for this. Something like crochet cotton would have been much more suitable.
Your pricing system has stunned me! I would have charged around five times as much. I have heard the story about how tough things are in an area many times in the past and that may be so, but my advice is to try to charge a price that is more in keeping with what other framers charge.
I think your material cost including wastage would be much higher than you have calculated!
-
- Posts: 367
- Joined: Wed 03 Oct, 2007 1:37 pm
- Location: Shrewsbury
- Organisation: Sutherland Arts & Crafts
- Interests: Photography
- Location: Shrewsbury
- Contact:
If this was needlework on a piece of fabric then I would not have used the wire for lacing. However the lattice material that forms the carrier for the wool knots is not really part of the artwork and indeed a lot may have been cut off had the tapestry been mounted on a stretcher frame and stapled.
I understand the need for using the proper materials and I am currently trying to source & stock a selection of needles, thread etc.
I have a mental picture of your business which goes something like "successfull, thriving, established, etc etc" and you have probably been in the business for a long time and work in an area that will support those kind of prices. If I charged 5 times as much I would get one job and be on the next stage out of town !!.
I understand the need for using the proper materials and I am currently trying to source & stock a selection of needles, thread etc.
I have a mental picture of your business which goes something like "successfull, thriving, established, etc etc" and you have probably been in the business for a long time and work in an area that will support those kind of prices. If I charged 5 times as much I would get one job and be on the next stage out of town !!.
Pat
-
- Posts: 1393
- Joined: Thu 23 Sep, 2004 8:31 pm
- Location: Detroit, Michigan USA
- Organisation: minoxy, LLC
- Interests: non-fiction knowledge
- Contact:
I agree with Osgood - wire is stronger that the fabric
Good things to stock in the shop for lacing are:
linen thread
button thread - cotton
regular heavy duty thread - cotton
Good things to stock in the shop for lacing are:
linen thread
button thread - cotton
regular heavy duty thread - cotton
Jerome Feig CPF®
http://www.minoxy.com
http://www.minoxy.com
-
- Posts: 1393
- Joined: Thu 23 Sep, 2004 8:31 pm
- Location: Detroit, Michigan USA
- Organisation: minoxy, LLC
- Interests: non-fiction knowledge
- Contact:
The above can be found in any good quality sewing shop.
The best needles that I have found that I use are curved darning needles. As in darning (repairing socks).
The best needles that I have found that I use are curved darning needles. As in darning (repairing socks).
Jerome Feig CPF®
http://www.minoxy.com
http://www.minoxy.com
Pat,osgood wrote:but my advice is to try to charge a price that is more in keeping with what other framers charge.
I was not advising you to charge what I charge. There are exchange rates to be considered anyway, so my pricing is not for you!
The above quote from my post is what I was advising for you to consider. If your closest competitor is in Inverness, and your quality is the same or preferably better, then your pricing only needs to be the same or just a small amount less than theirs. If customers have to travel any distance, then they would incur costs for that travel so you don't have to dramatically undercut.
As far as lacing is concerned, the current advice is to use a thread that is slightly weaker than the threads in the ground fabric.
If the piece had been stapled onto a frame, it would have been an incorrect practise to cut any of the ground 'lattice' off.
There is one over riding rule that should always be kept in mind when framing anything that is not temporary and worthless:
"Never do anything that cannot be totally reversed!"
We should never, cut, tear, glue, or otherwise interfere permanently with any item to be framed
If we follow that principle we will do no harm!
-
- Posts: 1102
- Joined: Fri 17 Mar, 2006 8:54 pm
- Location: Glandwr
- Organisation: Framing Mad
- Interests: Framing, watercolours & CCFC
- Location: Pembrokeshire
- Contact:
If you're worried about the thread failing there is another option. Machine stitch some material around the edge of the piece, then use saddlers thread to lace through that - this method gives more even support all round, allows you to pull the lace fairly tight, yet is easily reversible.
Wire is way too strong! It's likely to cut through the tapestry canvas in time....
Wire is way too strong! It's likely to cut through the tapestry canvas in time....
While I agree with that on principle, there is the very odd time when a customer brings a small piece of needlework on a large piece of cloth. (most of the time there's too little materialWe should never, cut, tear, glue, or otherwise interfere permanently with any item to be framed

How do you stand on washing needlework? I don't touch it, but if a piece is grubby I ask the customer to wash it, but explain how to do it.
We* will wash and press most needlework on cotton/linen etc, stitched with cotton and with no metallic threads, beads or other baubles. As long as they are new** and the thread is DMC or Anchor. We wouldn't wash anything on tapestry canvas mesh stitched in wool.Mary Case GCF wrote:
Boil wash with a bit of bleach and then tumble dry on maximum heat - hot iron.
KIDDING!!!
Soak in luke warm water overnight in something like bio-tex - but normal washing liquid - ariel etc is fine too - so is powder as long as you completely dissolve it first.
Dry naturally on a white towel over a rail. Press from the back - low iron through a cotton sheet.
Not saying 'do it' just what we do, and we do it all the time - it's only cotton - I have pullovers that are more likely to run or shrink than your average X stitch - my grandson has an action man I have christened 'Calvin'!!
It should have been washed before it got to you - and even if it looks clean and has not been washed, it still should be (unless dodgy fabric/threads have been used - DMC and Anchor are colourfast) it will still, at best, have grease from hands on it - visible or not.
It's an extra and we rarely charge for it - if the customer takes it away to wash they may wreck it or just not get around to it and you lose the job, or maybe spend longer than you could in the design stage.
* Edit - Dang! Pat is registered here now, did I say 'We' ?
More coffee dearest?
**We have washed quite old pieces brought in for re-framing that have been stuck down in some way or are otherwise marked - mainly embroidery on Calico - the last one earned me a great big hug - and I had nothing to do with it


Regards the too-large fabric - well, let's ask the same question for a 12x12 oil painting (to be stretched on battens) in the centre of a 48x48 canvas.
Lines have to be drawn sometimes - just don't do anything that is a big surprise to the customer.